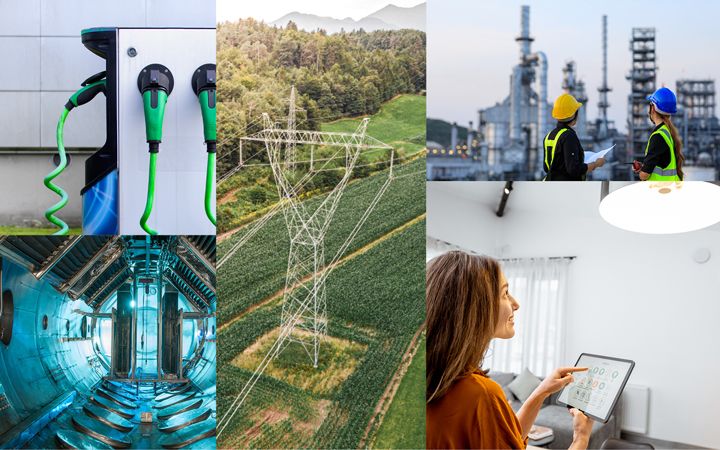
Examining the current and future economics of hydrogen energy
Hydrogen production costs today and potential evolution
Currently, the most widely used method in the mass production of hydrogen is steam methane reforming (SMR), referred to as gray hydrogen. SMR is a mature production process whereby high-temperature steam (700°C–1,000°C) is used with a methane source (such as natural gas) to produce hydrogen gas and carbon dioxide (CO2). There is approximately 9 kg of CO2 emitted per kg of hydrogen production. Gray hydrogen is used primarily for petroleum refining and ammonia production for agriculture fertilizer.
Industries are beginning to shift towards low emission or low carbon options for hydrogen production, often referred to as blue and green hydrogen, respectively. Steam methane reform combined with carbon capture and sequestration (CCS) technology is called blue hydrogen. Blue hydrogen in its current form captures anywhere from 50%-90% of the CO2 produced by the reform process. Meanwhile, green hydrogen produced via renewable or nuclear power generation through electrolysis is a zero-carbon production method.
Current hydrogen costs
Gray and blue hydrogen are favorable near-term alternatives to green hydrogen as the SMR and CCS technologies are currently more established and less expensive compared to the electrolyzer technology used for green hydrogen production. As both the technologies and economies of scale behind green hydrogen improve in the coming years, its production cost will likely become more competitive with that of blue hydrogen.
Hydrogen production cost projections
We have evaluated the methods and near-term opportunities for hydrogen production to develop a cost model.
Figure 1: Projected hydrogen production cost under several scenarios
In 2020, green hydrogen produced using solar power and electrolysis had a production cost of about $3/kg. The overall cost of hydrogen in 2020 came out to about $1.60/kg in curtailed energy and electrolysis scenarios. Our model estimates that blue hydrogen costs about $1.30/kg and that gray hydrogen produced via steam methane reform will cost roughly $0.70/kg in 2020.
While blue hydrogen is currently the least expensive option for low-carbon hydrogen production, our analysis demonstrates that green hydrogen may become cost-competitive with blue hydrogen within the decade, depending on the availability of curtailed or inexpensive renewable energy.
We have made several assumptions to inform our cost projections, detailed in Table 3.
Cost trajectories and technology learning curves
In addition to the assumptions articulated in Table 3, there are several other key considerations associated with industry developments and scaling of technology incorporated into the cost curves presented in Figure 1.
We often measure technological improvements by “the learning curve rate,” a number that represents a reduction in costs for each doubling of the cumulative number of units produced or capacity installed. Our analysis assumes a conservative 12% learning curve rate for green hydrogen technologies, whereas the Bloomberg NEF study from 2019 assumes a more robust learning curve rate of 18% to 20%.
With learning curve rates between 20-30%, solar photovoltaic (PV) technologies generally reside on the higher end of the spectrum; however, electrolyzer technologies have more in common with large-scale equipment such as wind turbines and conventional power than they do with extant solar technology. Wind turbines have a learning curve rate of about 12% to 20%. Processing facilities such as chemical plants and conventional power plants have learning curve rates between 8% and 12%.
The learning curve rate for the likes of gray and blue hydrogen will be minimal because both technologies already have years of prior research and development behind them. Therefore, our analysis assumes no learning curve rate for the gray and blue hydrogen cost estimate projections.
As technology costs come down for green hydrogen, the cost of renewable energy will emerge as a more important driver, as shown in the cost differential between no-cost curtailed energy and the renewable energy costs in Figure 1.
Other hydrogen cost considerations
Storage
The most common way to store hydrogen is in liquid tanks (or compressed cylinders for small-scale applications). As initiatives grow in many industries, hydrogen storage at scale will become critical, enabling its use in yet more industries. Existing fossil fuel infrastructure can play a major role in hydrogen storage and distribution. Namely, salt caverns can be repurposed for hydrogen storage and pipelines retrofitted to facilitate distribution.
Salt caverns
Storage tanks
For large storage applications, liquid tanks are another option. The principal cost to liquefy hydrogen is the 10 kWh of electricity per kilogram of hydrogen liquefied, which works out to about 60% of the total cost of liquid hydrogen storage. NASA and Kawasaki currently have large liquid hydrogen tanks, each of which can hold between 30 and 300 tons of liquid hydrogen. With this storage capacity, they can provide up to a week of fuel for a combustion turbine, assuming continuous operation and depending on the size of the turbine. These liquid tanks also have a boil-off rate of about 3% to 5% of capacity, although newer designs are expected to reduce the boil-off losses to as little as 1% per day.
Distribution
The U.S. and other countries with existing natural gas infrastructure may have the option to incrementally blend hydrogen into existing natural gas pipelines to avoid the capital costs of building a new transmission and distribution system for hydrogen. Although there are about 1,600 miles of dedicated hydrogen pipelines in the United States, the larger natural gas distribution and transmission lines do not currently accommodate any appreciable percentage of hydrogen.
There are a few potential technical and safety challenges with transporting hydrogen through pipelines, such as material construction concerns due to hydrogen embrittling metal at high pressures and leakage concerns due to hydrogen’s small size and flammable nature. Studies have indicated that natural gas transmissions lines have the technical capability of accommodating up to 50% hydrogen; distribution lines can accommodate up to 20%.
Hydrogen distribution quick facts and cost estimates
Currently, for distances greater than 500 km, costs for distribution are estimated by an International Energy Agency 2019 study as follows:
- Trucking gaseous hydrogen costs over $1/kg.
- Liquid cryogenic trailer transport is about $0.40/kg.
- Pipeline transport of pure hydrogen costs between $0.30-0.40/kg.
Assuming the demand for natural gas decreases over time, it is plausible that transmission pipelines may eventually transport 100% hydrogen using existing lines with limited modifications and lower pressures to mitigate embrittlement risks.
Hydrogen used in the transport sector is most commonly moved using compressed gas trailer trucks and liquid hydrogen tanker trucks. Small volumes are generally delivered in gaseous form and larger volumes delivered via liquid tankers. Liquid hydrogen tanker trucks have a lower cost per quantity of hydrogen transported which can offset the cost of liquefaction. Still, such trucks do experience boil-off losses so are not used for small volumes or multi-day trips.
Due to the costs involved in liquefaction, boil-off losses, and the time for bulk carrier transport over great distances, developers are considering converting hydrogen into ammonia or binding it to liquid organic hydrogen carriers (LOHCs) for transport then converting it back into hydrogen at its use point. The cost to convert ammonia back to liquid hydrogen is likely an additional $1.1/kg on top of the $0.40/kg for distribution over 500 km.
Conclusions
Blue hydrogen is a favorable near-term option for low-carbon hydrogen production. As electrolyzer technology becomes better-established and usage of renewable energy increases over the next 10-20 years, green hydrogen production will likely become dominant. Critical drivers of production costs often include the price of electricity for electrolysis and the price of natural gas for SMR processes. Additionally, the learning curve rate for electrolyzer technology paired with renewable energy significantly impacts total production costs. In the near term, pairing either curtailed or negatively-priced electricity with electrolyzer technology can effectively keep electrolysis cost-competitive with hydrogen produced through an SMR process with CCS—that is, keep blue hydrogen neck and neck with dirtier, gray hydrogen until renewable technologies are sufficiently advanced to eat into gray hydrogen’s market share.
The utilization of existing natural gas pipelines will likely be the most cost-effective option for hydrogen transport in the future but, for now, liquid hydrogen transported in cryogenic tanker trucks remains the most cost-effective option. Policy and regulatory developments could potentially reduce the estimated cost and thus accelerate the deployment of hydrogen in the energy and industrial sectors. With this industry-wide potential in mind, all eyes now fall to the federal government. If they choose to support burgeoning hydrogen technologies via a production tax credit or similar measure it could have significant and far-reaching impacts, not just on discrete projects’ economics, but on the overall cost of hydrogen today and far into the future.