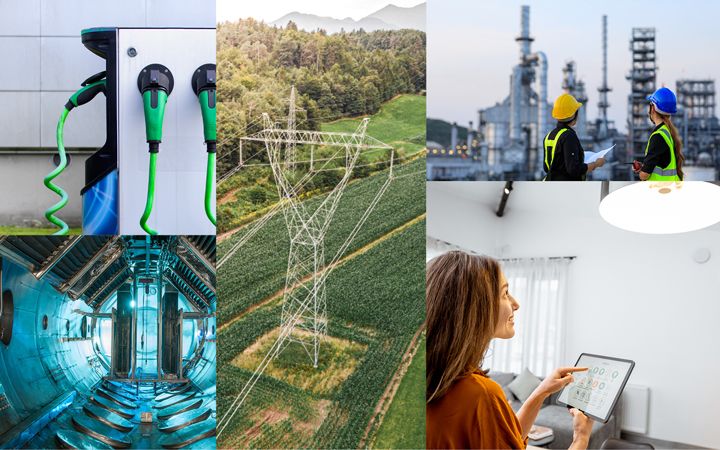
Retrofitting gas turbine facilities for hydrogen blending
Hydrogen provides solutions to reducing the power sector’s emissions, while continuing to utilize existing gas assets, as it can be incrementally blended with natural gas or used directly as a fuel in gas turbines to produce power.
Hydrogen can also be used as fuel in simple cycle or combined cycle facilities for peaking, or baseload operation, which can complement the intermittency challenges with power generated from renewable energy such as wind and solar technologies.
Many existing gas turbines can already operate with different ranges of hydrogen blending. For example, Siemens Energy’s aeroderivative gas turbine, SGT-A35, can operate with 100% hydrogen and General Electric has several B, E, and F class gas turbines with 100% hydrogen capability. Some gas turbine frames readily have the capability to blend high volumes of hydrogen with natural gas while other turbines require additional modifications to the turbine and balance of plant at a minor cost compared to replacing the entire turbine.
While NOx emissions may increase with higher blends of hydrogen with natural gas, 100% hydrogen provides a solution as it will produce little to no carbon emissions. A GE paper shows that currently a typical plant using 100% natural gas has a “carbon intensity of ~305–380 g/kWh.” If the plant switches to 100% hydrogen, the carbon intensity would become zero g/kWh. MHI is also working towards 100% hydrogen combustion with the development of its multi-cluster combustion turbines like the M501JAC and M701JAC to mitigate emissions and operability concerns such as NOx and flashback.
Plant retrofitting considerations
Most of the turbines that do not have high hydrogen blending capabilities will require a retrofit of certain plant components as well as new equipment to incorporate hydrogen as fuel. The following are some of the considerations for blending hydrogen in an existing gas turbine facility:
- Combustion section
- Fuel piping sizing changes
- Fuel piping system changes replacing flanged joints with welded joints
- Hydrogen offloading and fuel blending skid
- Gas turbine controls system upgrades
- Continuous emissions monitor system (CEMS) modifications or upgrades
- Safety sensors and leakage detectors HRSG furnace ductwork and selective catalytic reactor (SCR) modifications
- Air permitting changes or modifications
For the combustion section, the need to change out the combustor for high hydrogen blends is dependent on if the combustor technology reflects a diffusion system or a premixed system such as dry low emissions (DLE) combustors. The diffusion systems, where the fuel and air are introduced separately in the combustor, produce higher NOx and unburned carbon emissions with higher flame temperatures during combustion. The diffusion flame combustors have a wide range of fuel flexibility and therefore have better capability for hydrogen blending when compared to premixed combustor systems. Premixed combustors, where fuel and air are mixed before combustion, are a popular choice as NOx levels can be up to 100 times less than diffusion combustors. However, premix systems are more prone to instabilities in combustion dynamics and flashback or flame holding, especially when introducing a highly reactive fuel like hydrogen.
To accommodate high blends of hydrogen, a premix combustor may need to be inspected and replaced at a major maintenance interval. Manufacturers have introduced advanced premix combustion systems in order to allow improved premixing to support highly reactive fuels like hydrogen. Several turbine models have the option of changing out traditional premix combustor sections with the advanced premix technology with minimal changes to the major maintenance procedures for other turbine components. Updates to other components within the gas turbine will be dependent on the unit’s operation history and analysis of potential wear and tear in the hot gas path components when introducing hydrogen.
Downstream of the combustor or the gas turbine, the HRSG will need to be evaluated to accommodate the high temperatures of exhaust heat. Introducing hydrogen blends will likely increase flame temperatures and therefore will result in an increase in NOx emissions and exhaust gas temperatures. The SCR may also need to be modified to control NOx emissions depending on certain permits or regulation requirements.
Along with the combustor, the controls system will need to be updated with the introduction of a new fuel and new components. The fuel accessories are another plant level component to consider as new purge systems and fuel blending skids will be introduced. The piping to the turbine will need to be larger to allow more hydrogen flow due to the differences in volumetric flow and energy content between natural gas and hydrogen as mentioned in Table 1. Safety measures will also be included at the plant level with leak detectors and ventilation to ensure there is no leakage or fires.
Upstream of the turbine, there will likely be a hydrogen offloading station to bring hydrogen from storage to the fuel blending skid in the plant. New build gas turbine facilities for hydrogen blending will require no substantial retrofitting since many of the turbine and plant level considerations will already be considered.
Considerations for hydrogen implementation
While utilization of hydrogen in gas turbines has a few challenges compared to natural gas, blending hydrogen will allow for less carbon emissions. The NOx emissions can be mitigated by SCR modifications and combustion tuning for optimal operability. Gas turbine manufacturers are updating the premix combustion technologies to allow for higher blends of hydrogen, greater than 10%-50% of hydrogen by volume. Outside of the combustor, there are additional equipment and updates to existing equipment required at a plant level when introducing hydrogen. For example, new accessories such as piping and fuel skids, leakage detectors, and ventilation for safety concerns and HRSG and SCR modifications are some of the considerations when implementing hydrogen into a gas turbine facility.