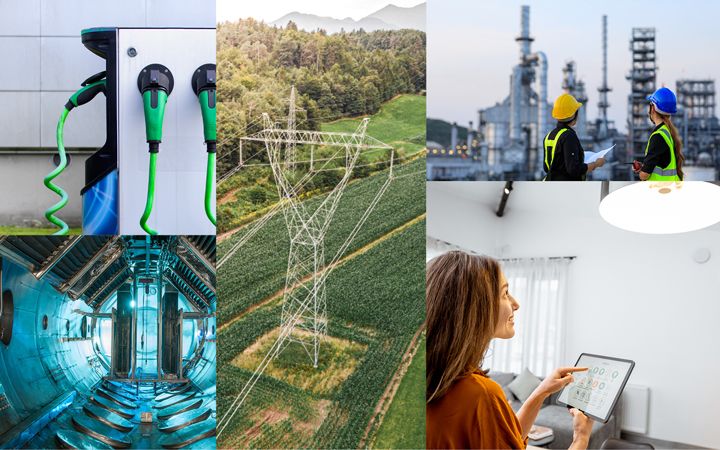
Recycling initiatives and carbon considerations that propel wind energy past other renewable sources
Recently, questions have been raised regarding the carbon footprint size of wind power. Some may recall a photograph circulating on social media of a landfill filled with used wind turbine blades. The implication of that photo being the wind power industry has a dirty secret; thus, traditional fossil fuel energy sources may be more environmentally sustainable. To help industry stakeholders make informed decisions, we gathered and evaluated key facts and metrics on the true cost of wind energy.
The recyclable—and non-recyclable—components of wind power
Wind facilities are typically comprised of wind turbines, which include major components such as rotor blades, a rotor hub, a nacelle, a generator, a tower, and a foundation. Plus, balance of plant equipment including cabling, various voltage transmission lines, civil works (including roads and fencing), and substation equipment.
Most wind farm components can be recycled or reused at the end of their useful life. According to a report from the National Renewable Energy Laboratory (NREL), wind turbines are comprised of steel, fiberglass, resin or plastic, cast iron, copper, and aluminum. With a total mass component breakdown of each wind turbine as following:
- Steel, used for towers and nacelles: 71%–79% of total mass
- Fiberglass and/or carbon fiber, wood, and resin or plastic, used for blades: 11%–16% of total mass
- Cast iron, used for hub: 5%–17% of total mass
- Copper, used for miscellaneous cabling, lighting, and protection systems: 1% of total mass
- Aluminum, used for miscellaneous components: 0%–2% of total mass
Turbine tower foundations are all concrete and steel, which can be razed, recycled, or reused as fill. Wind farm electric cabling and many other electric components can also be recycled as scrap metal. Wind turbine blades are one element of a wind farm that have posed a significant challenge at the end of their life. Historically, the only option was to cut the blades into smaller pieces and send them to landfill. As has been rightfully raised, that is not an ideal solution for the wind industry. In the past year some of the largest wind turbine original equipment manufacturers (OEMs) have taken on the challenge of blade recycling.
Siemens Gamesa Renewable Energy (SGRE) recently made a major step forward in the development of recyclable blades. The company announced it produced a fully recyclable offshore turbine blade using a new resin. Once heated by renewable energy, the resin can be fully separated from the blade’s other components making each component recyclable. The same turbine molds and materials can still be used with this resin as SGRE seeks to industrialize this process. This development comes after the company’s commitment to focus on recyclability and sustainability—including ensuring all turbine blades are 100% recyclable by 2030.
Other OEMs have followed similar courses of action:
- GE Renewable Energy recently announced a Blade Recycling Contract with Veolia to recycle blades from its onshore turbine fleet. Recycled blade material will be used for cement through a new kiln processing technology.
- Vestas announced earlier this year it will chemically separate composite fibers from blades’ resin so that glass and carbon fibers can be reused in the manufacture of new blades.
The carbon footprint of wind power
When evaluating if an energy source is environmentally friendly, it is important to consider the size of the source’s carbon footprint. The carbon footprint depicts the total greenhouse gases emitted throughout the lifecycle of the plant. Traditional fossil fuel energy sources result in significant carbon and other greenhouse gas emissions—on a continuous basis. Wind energy emissions can be traced to upstream construction and manufacturing with negligible emissions during operation. One way to determine the true impact of these emissions is to isolate the carbon footprint of each stage of operation.
The carbon footprint of a wind turbine is principally from the manufacturing and production of the turbine and foundation. Vestas and Siemens have both published lifecycle assessments over the past decade documenting the emissions associated with the construction and operation of their onshore wind plants. Each company cites manufacturing and sourcing of materials as the largest contribution to the upstream emissions of a wind farm—with only a combined 11% coming from installation and operation.
Steel and cement manufacturing can utilize significant amounts of energy, often derived from fossil fuels, but not always. Transportation and construction machinery in the wind energy supply chain are generally fossil fuel dependent. On average, Vestas and Siemens found that 25% of manufacturing emissions comes from the wind turbine tower, 26% comes from the foundation, and 12% from the blades. However, once a wind farm is operational, its carbon footprint becomes essentially nonexistent.
Recycling gives a return on emissions, with an average of 26% returned during decommissioning of a wind farm. That contribution is expected to increase as recycling processes are improved. In contrast, traditional coal or natural gas fired power plants have significant lifetime carbon footprints as they emit carbon and other greenhouse gases through combustion at each stage of their operational life.
Quantitatively, the carbon footprint of a typical wind farm is approximately:
- 99% less than the carbon footprint of a coal-fired power plant
- 97% less than the carbon footprint of a natural gas power plant
- 74% less than the carbon footprint of a solar energy farm
Despite some shortcomings, wind energy is indeed a green energy source. Recycling challenges are being proactively addressed to make wind energy greener and, as shown above, the carbon footprint of wind power is significantly less than most other energy sources. As the wind industry works to increase the sustainability of its operations, wind can only become greener.