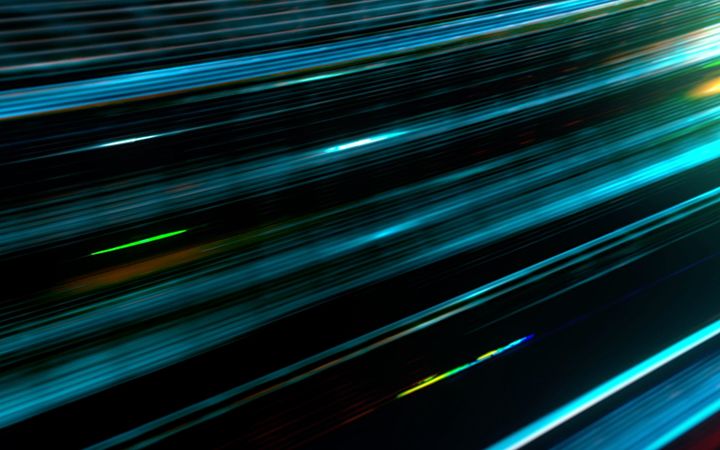
Using digital threads and twins to improve the MRO lifecycle
As an aircraft moves from manufacturer to operator to maintenance and into operations, a digital record of its full lifecycle is critical. But, differences in maturity with technology across stakeholders often leads to lost disconnected data and recording formats.
In recent times, the maintenance, repair, and overhaul (MRO) industry has been abuzz with discussions around digital threads and digital twins. These concepts may sound new, but the philosophies of the digital thread and digital twins have been in practice for some time. So what do they really mean, especially in the context of MRO?
The definition and history of digital twins and digital threads
Digital thread refers to a communication and data flow framework that allows an integrated view of a product or asset’s data throughout its complete lifecycle. A digital twin is the virtual representation of a product, asset, or system, which precisely mimics the physical object with current, as-built, and operational data.
Together, the digital thread and digital twin include as-designed requirements, validation, certification, and calibration records; as-built data; as-operated data; and as-maintained data.
It is commonly thought that digital twin technology was developed in 2002 when Michael Grieves coined the phrase at the University of Michigan. But, twinning has been a concept practiced by NASA since the 1960s. For example, NASA used twinning to assess and simulate conditions on Apollo 13, which was over 200,000 miles away. Back then, the “twin” was more of a physical rather than a virtual replica. But with the advent, maturity, and popularization of the Internet of Things (IoT) in recent years, digital twins have become even more pertinent and are prominently relevant today.
The phrase digital thread was coined at Lockheed Martin to describe using 3D CAD (computer-aided design) data to directly drive CNC (computer numerically controlled) milling or composite programming systems for carbon fiber placement. In both cases, the physical output is the result of an unbroken data link that comes from the original computer model of the respective part. The unbroken data path was the digital thread.
A consortium of aerospace and defense manufacturers gathered in 2011 to discuss the digital thread concept for the first time. The goal of their newly formed Computational Manufacturing Alliance (CMA) was to find common ground where both makers and users of the technology in need of a digital thread could work out data interchange issues.
The U.S. National Institute for Standards and Technology (NIST) works with stakeholders to advance the digital thread philosophy. It defines the digital thread as “a way for different machines in a manufacturing process to all follow the same set of digital instructions.” This definition is slightly different than Lockheed Martin’s original definition, but offers a more holistic perspective.
Applications of digital twins and digital threads for MRO
For simplicity, we define the digital thread as an unbroken cycle throughout the following phases:
- Ideate
- Design (or engineer)
- Manufacture (or produce)
- Operate
- Maintain (or service)
- Retire
Aircraft design and manufacture has been paperless since the 1990s. In comparison, Boeing conceptualized the 777 in 1990 and first rolled it off the production line in 1995 using 100% digital blueprints.
A full digital thread from ideation through to the first flight and delivery of the B777 aircraft continues to be a point of pride for Boeing. The B777 is frequently dubbed the “most successful aircraft in aviation.” Throughout the prototype production—and for all subsequent aircraft—digital twins with digital threads (up to Boeing’s handover to operators) exist.
The ideate, design, and manufacture processes are more digitally mature than the operate, maintain, and retire processes.
In fact, there is a noticeable drop in the digital thread maturity between the Manufacture and the Operate functions in the cycle—and another between the Operate and the Maintain functions, as shown below.
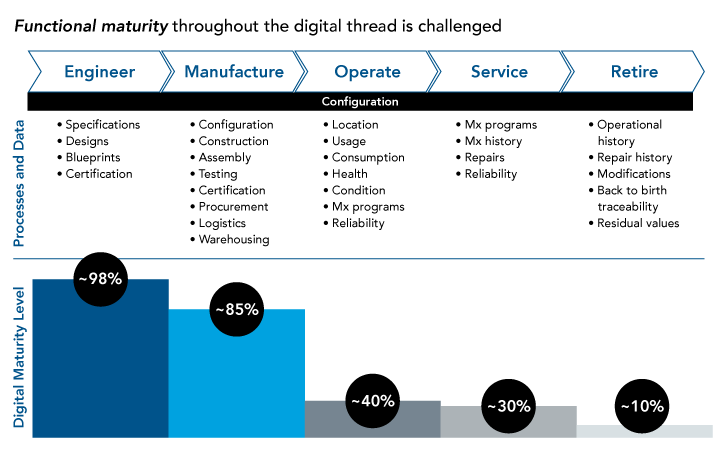
A desire to improve MRO IT solutions
In a 2019 Cap Gemini survey of “Digital Aviation in MRO” conducted through the Aircraft Commerce and AircraftIT community, respondents reported:
- 87.4% noted their current MRO IT solutions are average or below average.
- 78.1% reported that there is significant value from closing gaps in the digital thread.
- 76.9% acknowledged that value would be received if OEMs (original equipment manufacturers) close the digital thread gaps.
As such, we can conclude:
- There is a desire to improve current MRO IT solutions to “above average.”
- Improvements will come from addressing the digital thread.
- OEMs are seen as a critical resource to the digital thread solution.
A quick look at MRO IT system purchases over the past 10 years shows that more than 850 airlines globally have made significant technology investments to modernize systems. Most of these airlines are now on systems that are still active in the marketplace, supported, enhanced, and developed.
Are the known needs, illustrated by the survey responses noted above, because such systems are still catching up to the digital thread? Or because the operators have not yet fully adopted such systems?
Is the perception that the OEMs are key contributors to closing the digital threads also the reality? The OEMs are already very mature in making aircraft and engines. The real challenge is how can this translate to operations and maintenance.
So, is the digital thread not the primary responsibility of the airlines, operators, and MROs? Or is the challenge that it’s there—already provided by the OEMs—but airlines and MROs don’t have access?
Existing gaps between manufacturing and operations in the digital thread
Digging further into the divide between “manufacture and operate” and “operate and maintain,” a few noteworthy patterns emerge.
Operators have always focused on good configuration control and maintenance programs management as important functionality when selecting MRO IT systems. I would like to focus on just those two aspects, although there are numerous other possible gaps.
Aircraft readiness logs (ARLs) are now produced automatically from RFID (radio frequency identification) and AIDC (automatic identification and data capture) data on components assembled into the aircraft. A typical Airbus aircraft has 5000+ components, and a Boeing aircraft has 7000+ such parts. The ARL is a crucial document that is handed over from the OEM to the operator. Enhanced data and new generation aircraft also include LSAPs (loadable software aircraft parts) information. These include as many as 300 parts with 1400 software instances for a single B787 aircraft.
The ARL is vital to setting up an aircraft in any operator’s MRO IT system. How this is handed over and how it is ingested has many variations in actual practice across operators.
Operator standardization is lacking even with the same MRO IT system and the same aircraft type and model across organizations. For example, position assignments (or position codes) for the same part numbers on an Airbus A320 series aircraft configuration will differ between any two operators with the same MRO system.
The current maintenance planning document (MPD) and the maintenance review board report (MRBR) for any aircraft type are based on Maintenance Steering Group (MSG-3 ) philosophy that is now 30 years old. The MPD and the MRBR are critical documents used to create the operator’s maintenance programs (OMPs). Although ECM (engine condition monitoring) and AHM (aircraft health monitoring) have both been around for quite a while, none of the MPD tasks are of AHM or ECM type. Inbuilt sensors and data now change the nature and value of the tasks in the MPD and consequently the OMP.
Additional documentation and manuals delivered with aircraft—including the AMM, IPC, WDM, SRM, and so on—also vary by operator or maintainer in the way they are ingested and processed into internal MRO IT systems. Keeping up with revisions is often lagging, and tasks sources content varies for any OMP. Some may have seamless linkages between manuals (for example, MPD task linked to OMP and AMM, which in turn is linked to the IPC) and some may have pure PDF execution documents only.
These scenarios demonstrate how easily the digital thread is broken during key handovers from manufacturing to operations and maintenance.
Is it possible, then, that we are trying to manage digital assets using conventional and traditional methods and systems? Is there another way to look at this continuity issue?
The path forward involves incremental improvements and collaboration
IP (intellectual property) between OEMs and the MROs is an ongoing discussion. In February 2018, IATA and CFM signed a pro-competitive agreement that allows licenses to use CFM manuals and repair methodology content even if non-CFM parts are involved.
In September 2019, Airbus announced that it would charge the MROs a royalty fee on top of access fees for using its technical data. This was quickly retracted when met with resistance from the industry.
Owning and controlling the service, maintenance, and upgrades for aircraft and associated equipment is big business that can last 20+ years, depending on the product. At stake are millions of dollars of annual maintenance—either revenue that manufacturers can gain by servicing what they build, or expenses that owner-operators or MROs can re-capture by obtaining information needed to maintain their assets themselves.
Until there is openness, collaboration, and sharing, this will continue to be an area of conflict.
From a systems standpoint, there is merit in reviewing digital assets management from PLM (product lifecycle management) and EAM (enterprise asset management) standpoints since these have already been proven in the front-end processes. Inheriting the existing digital thread and twin for new aircraft deliveries is likely faster and cleaner than re-creation in traditional MRO IT transactional systems.
This is also related to how much IP the OEM will share through the same IT systems. For certain, the vendors that support the MRO IT systems should also look at standardizing implementations for configuration control and maintenance programs.
Perhaps it is also time for an MSG-4, which acknowledges the complex network of sensors, data, IoT, and connectedness that comprise modern aircraft. To forge a successful path forward, we must seek incremental improvements and collaboration.